Technology transfer
Capabalities
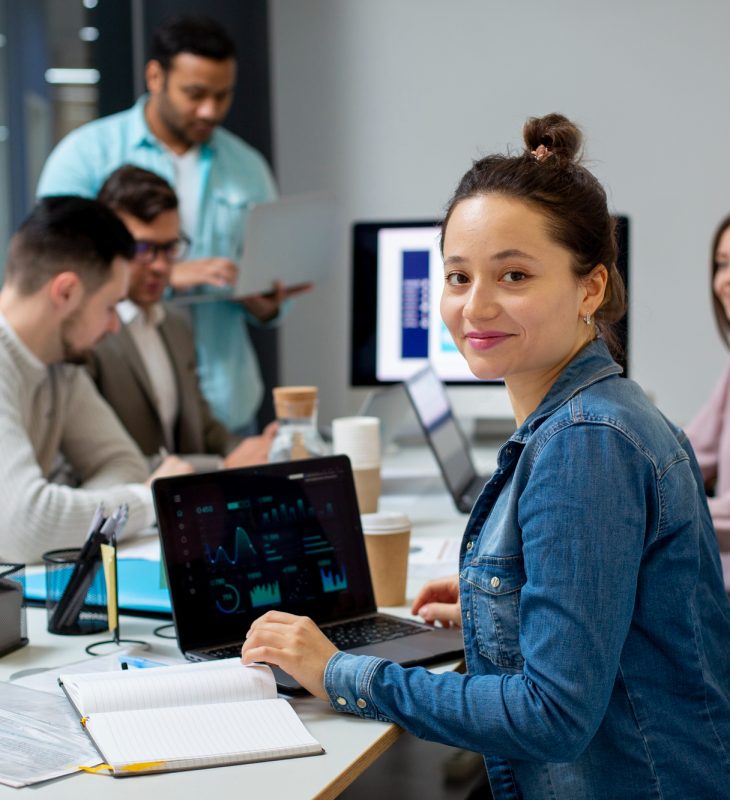
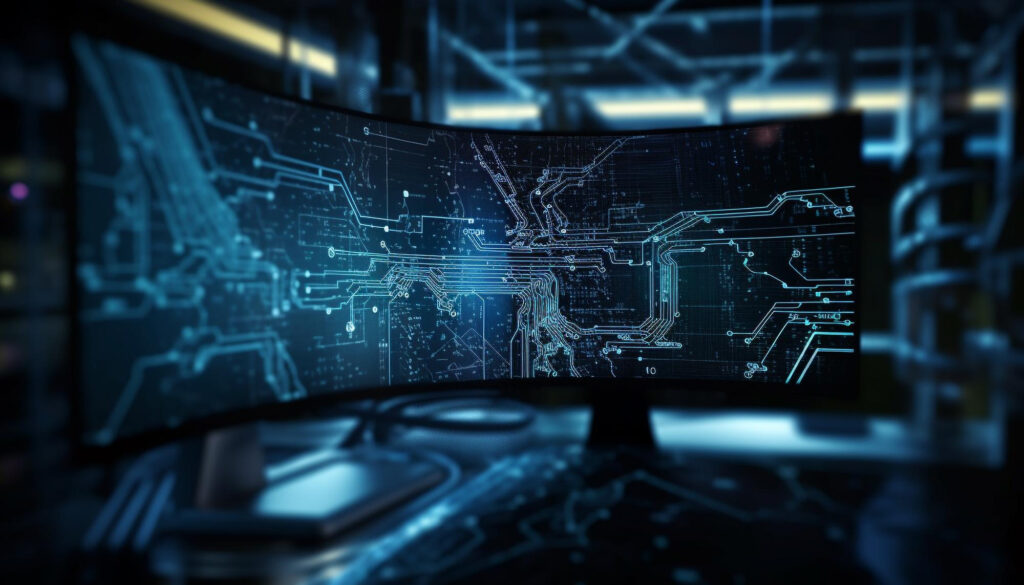
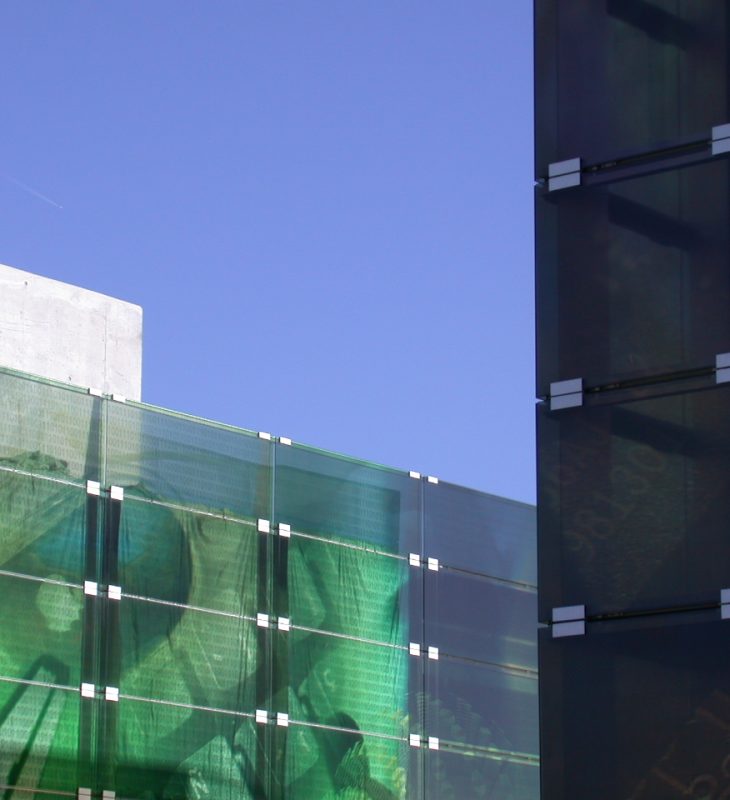
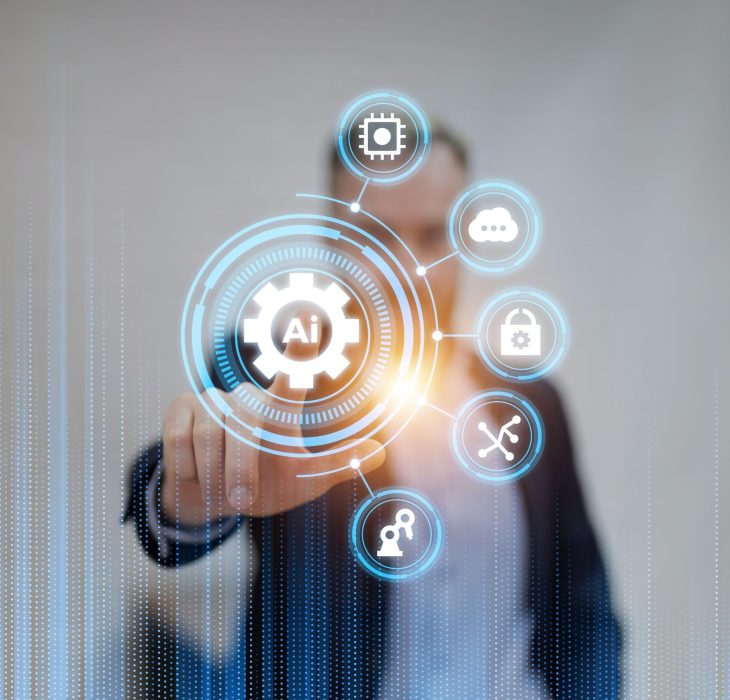
Decisional system analysis and design
In a business organization, the so-called Decisional System is basically composed of decision-making processes, characterized according to their short-, medium- and long-term impact (Operational, Tactical and Strategic). There are often coordination problems in this area between the different areas of the company. In this sense, CIGIP performs analysis of the map of decision making centers in a company, in order to detect points for improvement. It also has extensive experience in the design of the most appropriate decision-making system for the company’s activity. With the analysis of the decisional map of a company and the simulation of the decision making activities, the coordination problems between the different areas of the company are determined, at the same time that the optimization of the decision making activities and the elimination of overloads in certain decision makers is achieved.
Analysis and design off performance management system in a company and/or supply chain
Organizational performance management is increasingly becoming an element of competitiveness and differentiation between those companies that are capable of doing it and those that are not. Moreover, they must be able to do it in a simple, continuous and effective way in order to compensate for the effort invested in this process. In today’s competitive environment, one of the key factors associated with success is the ability to measure and manage performance in the different facets of an organization’s management. CIGIP’s experience of more than two decades in this line, analyzing, designing, developing and implementing performance management systems, allows us to adapt to all types of organizations, regardless of their size and sector of activity.
Advise on ERP software selection
ERP systems (Enterprise Resource Planning) are integrated management systems for the company. The ERP are products that involve a high investment by the company and of which there is a great variety of packages offered. CIGIP has extensive experience in the analysis of management systems, offering companies an analysis of business processes and capture of requirements, as well as the analysis of the ERP pre-selected based on the requirements and quantification of the adaptability of each ERP to the company. In this way the researchers of our center offer reliable advice for the selection of the most appropriate ERP for each organization through a quantitative analysis of the different alternatives for the correct decision making.
Production/operations management in a context on uncertainty
Order management processes and order commitment are critical in the sales and customer relationship. A bad approach or design can deteriorate customer service or create unnecessary urgencies or inefficiencies in the development of industrial operations (manufacturing/assembly/warehousing/distribution/installation). Our researchers will help you design order management and order commitment processes for each particular situation, taking into account both traditional single-company scenarios and collaborative scenarios in sales networks of complementary product/service packages.
Dirección de Producción/Operaciones en contexto de incertidumbre
Models for production and operations planning that do not recognize uncertainty can be expected to generate inferior planning decisions compared to models that explicitly take uncertainty into account. Due to the unavailability and uncertainty of information it is extremely difficult to generate plans under a dynamic environment. Our position is that fuzzy set theory and possibility theory are, in general, a suitable methodology for current production and operations planning systems. The design and implementation of fuzzy mathematical programming models to solve production and operations planning problems under conditions of uncertainty can be a major breakthrough in business.
Advanced design of production system
Some companies encounter peculiar problems in their production system, such as uncertainty in the layout design variables or uncertainty in the product mix. These peculiarities imply a non-conventional, non-commercialized, non-standard design. CIGIP uses advanced techniques for the design of these systems that allow adjusting the Production System to the existing needs.
Design of advanced production of scheduling system
There are companies with specific problems in their production system that, due to their complexity (relationships between resources, size, dynamicity, uncertainty, etc.), imply a non-conventional, non-commercialized/non-standard production scheduling. CIGIP has extensive experience in the development of algorithms and implementation of software tools, which in turn are integrated with the tools used by the companies. This provides an advanced solution to the problem of production scheduling that favors cost reduction and improved compliance with delivery deadlines.
Design and implementation of production management system
The management of the production activity is one of the most complex tasks developed within the company. It is necessary to use Production Management models adapted to the needs and characteristics of each company. From the classic Production Management models such as MRP, JIT and OPT, a particular adaptation to the production environment of each company is necessary. The definition of an adequate Production Management system guarantees the success in the achievement of cost, quality, delivery time, etc. objectives, and is an indispensable step for the selection and implementation of a computerized Production Management package.
Modeling and simulation of production processes
Changes in production systems result in the decision to select a series of possible alternatives that imply different degrees of investment and achievement of objectives. Simulation makes it possible to make models of production processes that are very close to reality. Simulation models help in the selection of alternatives based on the observation of the dynamic evolution of the system and on the results obtained.
Collaborative forecasting in supply chain
One of the most influential decision-making processes in a company is demand forecasting. Accurate forecasts help to provide better customer service along with a reduction in inventory levels. The level of forecasting accuracy depends on the company’s ability to obtain relevant information and interpret it. Collaborative Forecasting is based on the fact that each of the companies that are related to each other (customers and suppliers or nodes of a supply chain) has relevant information for forecasting that the others do not have.
Reengineering of supply chain operations
CIGIP has developed a methodology for the analysis and improvement of operations in a supply chain through alignment with the company’s vision and mission, modeling of the current and proposed system, implementation of the adopted solutions, monitoring, evaluation, control and continuous improvement.